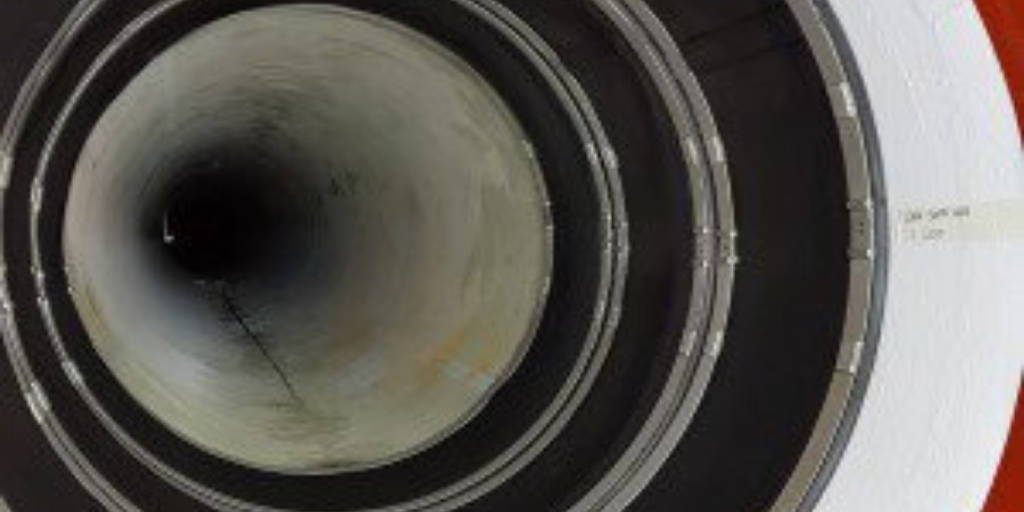
Rehabilitación de tuberías de agua potable de gran diámetro con manta autoportante (y II)
Lunes, 25 Mayo, 2020En la segunda parte del artículo del número 415 de Cimbra, se analizan las especificaciones estructurales de los trabajos llevados a cabo en Sant Quirze del Vallés, Barcelona, para la rehabilitación de la arteria PTLL-C250 de Ens d’Abastament d’Aiga Ter-Llobregat.
De esta manera, el diseño del tubo curado “in situ” de Insitumain (marca registrada) se llevó a cabo según las normativas ASTM F1216. Previo a la instalación, se realizaron:
- Tres arquetas. Una arqueta de seccionamiento y dos de derivación.
- Cinco pozos de ataque para la introducción-extracción del tubo curado “in situ”.
- Un by-pass de tubería de PEAD de 100 metros de longitud.
- La longitud total de la actuación se ejecutó en cinco instalaciones.
- De la cámara E3 al codo con una longitud de 158 metros.
- De la cámara E1 a la cámara de seccionamiento de 177 metros.
- De la cámara E1 a la cámara E2 de 235 metros.
- De la cámara E2 a la cámara del margen derecho de 47 metros.
- De la cámara del margen derecho al codo de 59 metros.
La primera instalación, desde la cámara E3 al codo, se instaló el 20 de febrero de 2019, con una longitud de 158 metros y una diferencia de cotas en la rasante del tubo entre el inicio y el final de la instalación de 5,58 metros.
La semana siguiente, el 27 de febrero, el equipo de rehabilitación se trasladó a la cámara E1 para instalar la segunda, desde la cámara E1 hasta la cámara de seccionamiento, con una longitud de 177 metros y una diferencia de cotas en la rasante del tubo entre el inicio y el final de la instalación (-1,56 metros).
Desde la cámara E1, se instaló, el seis de marzo de 2019, el tramo más largo del proyecto desde la cámara E1 hasta la cámara E2, con una longitud de 235 metros y una diferencia de cotas en la rasante del tubo entre el inicio y el final de la instalación de 3,13 metros.
Las dos últimas instalaciones se realizaron desde la misma cámara (la cámara del margen derecho). La primera de ellas, se llevó a cabo hasta la cámara E2, con una longitud de 47 metros y una diferencia de cotas en la rasante del tubo entre el inicio y el final de la instalación de -1,38 metros se instaló el 13 de marzo de 2019.
Finalmente, la última instalación del proyecto se llevó a cabo el 20 de marzo de 2019, con una longitud de 59 metros y una diferencia de cotas en la rasante del tubo entre el inicio y el final de la instalación de 0,61 metros.
Con esta última instalación, se completaron los 676 metros en cinco semanas. La técnica elegida en esta obra por Insituform Technologies Ibérica, S.A., fue mediante reversión y calentamiento con agua, por ser la tecnología que mejor asegura el control preciso de la temperatura de endurecimiento de la resina y su óptimo curado.
La presión hidrostática
La tubería continua flexible se instala mediante reversión gracias a la presión hidrostática ejercida por la columna de agua creada con la suma de la profundidad de la conducción y la altura de la estructura de inversión. Este fluido es el que ejerce la presión necesaria al tubo continuo flexible para que se ajuste perfectamente en todo el desarrollo circunferencial de la tubería existente.
El mismo fluido utilizado para la instalación se aprovecha para el calentamiento. Esto se consigue con un sistema de recirculación a través de una caldera de agua sobrecalentada, en la que se alcanzan los 80 grados centígrados. La temperatura del fluido es transferida a la resina termoendurecible, provocando así una reacción exotérmica en sus moléculas y consiguiendo su endurecimiento “in situ”.
En tuberías de presión, es aún más importante asegurar el correcto curado de la resina. No es conveniente que se alcancen altas temperaturas que provoquen un gran estrés térmico, ya que puede traducirse en tensiones internas y provocar grandes retracciones, microrroturas en la pared del nuevo tubo o reducción de las características mecánicas.
Para ello, el calentamiento con agua ofrece un control más precio, no solo a lo largo de toda la longitud, sino también a lo largo de toda la sección, no variando entre parte altas y partes bajas de la conducción.
El calentamiento se controla mediante un sistema centralizado que registra datos de temperaturas cada 10 centímetros en tiempo real, gracias a las propiedades de la fibra óptica.
Este sistema ofrece una gran capacidad de adaptación a las condiciones especiales de cada instalación, asegurando la calidad y la robustez del producto final, puesto que garantiza la trazabilidad del proceso de calentamiento y curado.
Una vez terminada la instalación y curado de cada tramo, se consigue un tubo sin ningún tipo de junto a lo largo de toda su longitud. Se evita así el riesgo de fuga que pueden causar dichas juntas (los puntos más vulnerables de la red).
Los puntos extremos, tanto al inicio como al final, se solucionan con juntas internas que aseguran la estanqueidad del tubo curado “in situ”. Estas juntas internas están construidas con EPDM (Etileno Propileno Dieno tipo M ASTM) y dos aros de acero. Éstos últimos se instalan mecánicamente solapando, por una parte el tubo continuo curado “in situ” y, por otro, la tubería existente.
Objetivos
Para ATL, la colocación de la manga reversible Insitumain ha cumplido ampliamente los objetivos marcados en el proyecto inicial:
- La afección al entorno ha sido mínima.
- Los procedimientos de trabajo se han basado en una monitorización en continuo de parámetros como la temperatura y la humedad relativa. Esto ha permitido seguir escrupulosamente los gradientes de variación de dichos parámetros, así como los tiempos de curado. Todo ello repercute en una buena calidad del producto acabado.
- El producto acabado presenta un excelente aspecto y es apto para transportar agua para el consumo humano.
- La utilización de este sistema ha resultado más económica que si se hubiera llevado a cabo la tradicional sustitución de tubería.
- Se ha asegurado la fiabilidad del funcionamiento de una arteria principal de la red de abastecimiento de ATL.
Autores: Andrés Dueñas Jurado (Ingeniero Industrial y Jefe de Mantenimiento de Red ATL) y Raúl Martín Domínguez (Ingeniero Técnico de Obras Públicas, Ingeniero de Canales, Caminos y Puertos y Director de Operaciones en Insituform Technologies Ibérica).
El artículo completo se encuentra en el número 415 de Cimbra.